
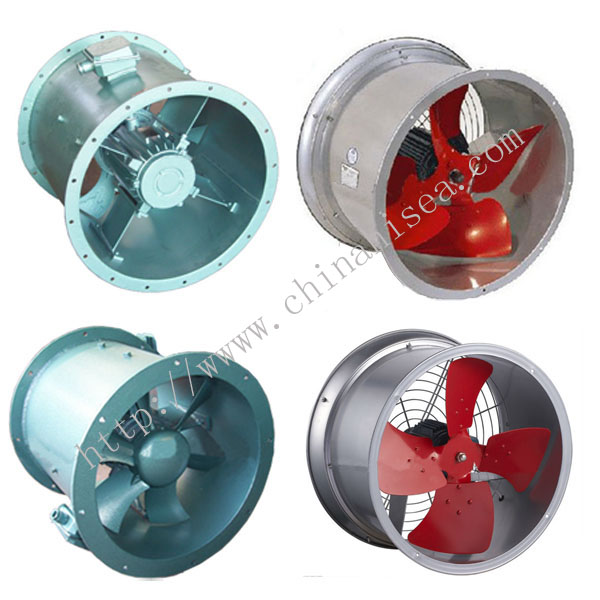
Figure 10.1: Schematic of a typical centrifugal pump The pressure within the fluid increases accordingly. The fluid’s kinetic energy increases due to the energy added by the impeller and enters the discharge end of the casing that has an expanding area (point 2 in Figure 10.1). The impeller rotates within its casing and sucks the fluid through the eye of the casing (point 1 in Figure 10.1). andĪ centrifugal pump consists of a rotating shaft that is connected to an impeller, which is usually comprised of curved blades. Suitable for being driven from high-speed prime movers such as turbines, electric motors, internal combustion engines etc.Ability to operate against a variable head.Simplicity of construction – no valves, no piston rings, etc.Centrifugal pumps have several advantages over other types of pumps, including: Centrifugal pumps are most often used in water and wastewater systems, making it important to learn how they work and how to design them. The components and design of a pumping station are vital to its effectiveness. The most previous numerical studies were focused on the design or near-design state of pumps.In waterworks and wastewater systems, pumps are commonly installed at the source to raise the water level and at intermediate points to boost the water pressure.
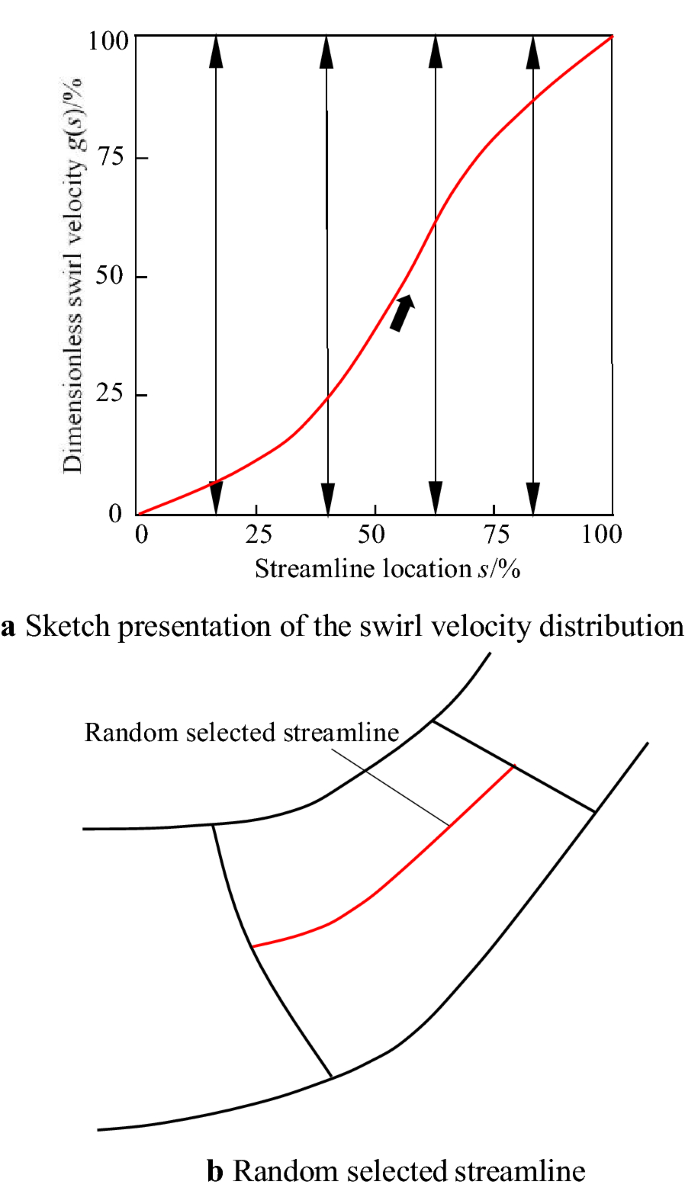
Centrifugal pumps are widely used in many applications, so the pump system may be required to operate over a wide flow range in different applications. The fluid enters the pump impeller along or near to the rotating axis and is accelerated by the impeller, flowing radially outward into a diffuser or volute chamber (casing), from where it exits. The rotational energy typically comes from an engine or electric motor. Centrifugal pumps are used to transport fluids by the conversion of rotational kinetic energy to the hydrodynamic energy of the fluid flow. Introduction: Centrifugal pumps are a sub-class of dynamic axisymmetric work-absorbing turbomachinery. CFD analysis was performed for the impeller vane profile and pump characteristic curve is obtained by using Ansys Fluent. Impeller vane profile was generated by circular arc method and point by point method. Impeller is designed for the head (H) 40 m discharge (Q) 28 L/s and speed (n) 1470 rpm. In this study, Computational Fluid Dynamics (CFD) approach was suggested to investigate the flow in the centrifugal pump impeller using the Ansys Fluent. Design and development of turbo machines like centrifugal pump is highly complex due to turbulence flow structure, unsteadiness and cavitation inside the pump. more Centrifugal pumps are the most commonly used in different fields such as industries, mining, agriculture etc. Centrifugal pumps are the most commonly used in different fields such as industries, mining, agri.
